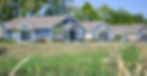
MODULAR
RESOURCES
& NEWS
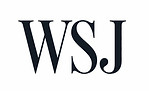
AMERICA'S BIGGEST APARTMENT OWNER TAKES A LEAP INTO MODULAR
Gregstar Real Estate Partners is opening a six-building modular apartment complex, complete with a gym, amphitheater and bocce courts. It is Greystar's first US project assembled using this alternative construction method, aiming to combat the chronic delays of traditional construction.

FORT WAYNE TESTS MODULAR CONSTRUCTION
This year four new housing types are being constructed in Fort Wayne’s East Central Neighborhood as part of the Innovative Housing Showcase project from the City of Fort Wayne. The project will test new approaches to how houses are built and used in the Fort Wayne housing market. READ MORE
VOLUMOD PARTNERS WITH NATIONAL BUYERS GROUP LMC
Volumod is partnering with LMC, a national buyer’s group, to bring billions of dollars in buying power to bear on our prices! During the depth of the Great Depression, a lumber dealer pitched the idea of group buying to his colleagues in the industry. Today, LMC is a leading forest products and building materials buying group representing nearly 450 Dealers with over 1,900 locations in all 50 states. Learn more about the buying power of LMC and how you can benefit. LEARN MORE

ALL PATHS LEAD TO MODULAR
“Traditional home construction means building a home, stick by stick, outdoors…This process wastes time, wastes effort, and creates excessive waste for landfills. There are many other reasons that the old way of building isn’t the way forward.” READ MORE
THE (SURPRISINGLY LONG) HISTORY OF MODULAR CONSTRUCTION
The idea of modular has been around for a long time. In colonial times, folks would have buildings disassembled in England and reassembled on this side of the pond. And, a hundred years ago, Sears Roebuck and Co. even got into the modular game, shipping pre-constructed homes via railroad. However, nowadays, “New technology, like better construction cranes, have allowed modular buildings to be built bigger, taller, and in many designs. Units can be shipped across the country and can be put together on-site in a matter of days.” MORE: THE MODULAR BUILDING INSTITUTE
WHY PRIVATE LENDERS ARE EMBRACING MODULAR CONSTRUCTION
Alternative lenders are seeing an increase in multifamily deal prospects as institutional lenders tighten their underwriting standards or sit on the sidelines. Not every transaction or development proposal passes muster, however. One strategy that is getting a fair amount of interest from these lenders is modular construction. Pre-fabricated modules are cost-effective and allow for faster construction times. They are also highly flexible, which helps mitigate risk and allows for quick adjustments to changing conditions. MORE FROM MULTI-HOUSING NEWS

MAKING MODULAR
CONSTRUCTION FIT
The case for modular construction in the US is clear...Industrialized production methods allow companies to optimize material utilization, reducing waste. Fitting modules together on site is quicker and requires less labor than traditional construction methods. McKinsey analysis suggests that modular techniques could allow home builders to accelerate end-to-end project timelines by 20 to 50 percent while reducing costs by up to 20 percent. Moreover, modular projects may be easier to execute on urban job sites since they require less space for the storage and preparation of materials...Despite these apparent benefits, the approach has struggled to gain acceptance in North America. READ MORE
MODULAR BASICS: MODULAR MATH 101
In modular construction, single-family and multifamily homes, as well as commercial properties, are built offsite (typically indoors to eliminate weather-related delays), then delivered to a site and set on a foundation...But while saving time with modular construction is appealing, some property owners and developers might be left wondering if time saved translates into money saved.
MORE FROM OFFSITE BUILDER
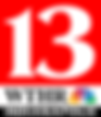
INDIANAPOLIS COMPANY HELPS FIND JOBS FOR FORMERLY INCARCERATED

MODULAR MARKET: INDIANAPOLIS COMPANY SEES SIGNIFICANT OPPORTUNITY IN AFFORDABLE HOUSING
A 2-year-old company on the east side has its sights set on tackling central Indiana's affordable housing problem through modular construction.
MORE FROM THE INDIANAPOLIS BUSINESS JOURNAL
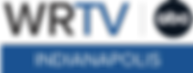
RE-ENTRY PROGRAM PROVIDES HOPE TO THE FAR EASTSIDE AND BEYOND
Inside of a warehouse on the far northeast side, employees at Volumod are building modular homes.
"I prayed for something like this; I never thought I will find it at 30th & Post Road," Kevin Caldwell said. Caldwell served 32 years in the Department of Correction... MORE FROM WRTV INDIANAPOLIS

$114 BILLION IN MODULAR CONSTRUCTION PREDICTED
Modular multifamily construction—where construction happens primarily off-site—is growing rapidly. One forecast shows that modular construction generally will be a USD $114.78 billion industry by 2028, with a compound annual growth rate (CAGR) of 6.1% between 2021-2028. In 2020 the modular construction industry was valued at $72.11 billion. Another estimate states that this industry will grow faster, to $160 billion by 2023...
MORE FROM SWIFTLANE

WHY CHOOSE MODULAR CONSTRUCTION?
As every professional in the building industry knows, construction can be a costly and endlessly time-consuming endeavor. Delays are almost more frequent than on-time construction, and can be induced by extensive bureaucratic requirements, weather and other unexpected circumstances, inadequate planning, too few personnel, or a whole host of other causes. MORE FROM ARCH DAILY...

DEMAND FOR PREFABRICATED APARTMENTS CLIMBS AS COSTS BALLOON FOR MULTIFAMILY DEVELOPMENT
Construction of prefabricated homes is ramping up and providing an alternative to traditional multifamily, where the construction process has slowed because of rising costs and supply-chain delays...
MORE FROM THE WALL STREET JOURNAL

WELCOME TO PREFAB'S MOMENT
The COVID-19 pandemic has turned our world upside down, shifted priorities, and helped push forward many ideas that were once considered “alternative.” Prefabricated building is no exception. As people rush to build larger homes, second homes, or additions to existing homes, demand is spiking for what are often considered faster, cheaper, more flexible, and more predictable building methods...MORE FROM ARCHITECTURAL DIGEST

THE FUTURE OF MODULAR AFFORDABLE HOUSING
The need for new apartment units is increasing in the Northeast and across the nation. High construction costs, however, present a major barrier to creating enough affordable housing supply. Modular homes have the potential to reduce construction timelines and costs, making them ideal for affordable housing solutions. These buildings have caught on in Japan, Scandinavia and other parts of the world, but not in the U.S. What’s holding us back? MORE FROM JP MORGAN CHASE

IS MODULAR CONSTRUCTION THE FUTURE OF MULTIFAMILY HOUSING?
If you didn't know anything about its history, the building at 193 Henry Street on Manhattan's Lower East Side may seem like your average new luxury condo on the block. However, there is something quite unique about how it was built that just might spark a trend in the city. As first reported by Curbed earlier this month, the six-story building named Idylls recently topped out, becoming the first luxury condo in Manhattan to be built using modular construction....MORE FROM COOPERATOR NEWS

MULTIFAMILY MODULAR CONSTRUCTION TOOLKIT
The high cost of developing multifamily housing is a major contributor to the nation’s affordable housing supply crisis. To try and resolve the lack of affordable housing, various cost drivers throughout the life cycle of a housing development — from pre-development planning and land purchase, to the construction phase, to projected operating expenses — are being re-evaluated to find opportunities for both time and cost savings.
DOWNLOAD TOOLKIT FROM FANNIE MAE
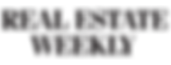
ONE OF THE LARGEST MODULAR MULTIFAMILY PROJECTS SELLS
OneFive Capital, a Philadelphia-based real estate company, has purchased one of the country’s largest modular multifamily buildings “Next LVL,” a Class A, 281-unit building in the University City neighborhood of Philadelphia for $88 million. OneFive plans to rebrand the development as “SOLO on Chestnut“...
MORE FROM REAL ESTATE WEEKLY